A Glimpse inside the Toyota Higashi-Fuji Technical Center Facilities |
|
|
 |
 |
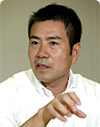 |
 |
Project General Manager:
Yoji Nagai |
|
The following is a brief look inside Toyota’s Research Labs
The Role of the Higashi-Fuji Technical Center
Toyota Motorsport GmbH (“TMG”) focuses complete attention and effort on one goal-the next race. And it’s the support of the staff at the Higashi-Fuji Technical Center, conducting research and development using the full resources of mighty Toyota Motor Corporation, which helps TMG get the job done. TMG works the front line of the battle, with the Higashi-Fuji Technical Center providing air cover. Without the combined efforts, Toyota’s F1 activities would never get off the ground.
Please tell us about the role of the Higashi-Fuji Technical Center
Yoji Nagai, Project General Manager, Motor Sports Division:TMG maintains laser-like focus on their racing activities. Even five or 10 more horsepower can mean the difference between being competitive or finishing last, so it’s the role of the Higashi-Fuji Technical Center to do the research that finds that extra bit of power. We conduct research into basic principles, asking ourselves questions such as what configurations could make combustion more efficient. What we find, we apply to the racing group at TMG.
Are research activities limited strictly to engine development?
Nagai:Early on, we put everything into engine development. But we decided this wasn’t enough, so we also undertook chassis development. With the chassis, our main focus is on aerodynamics and movement analysis.
|
What types of technical backgrounds do staff members bring to the Higashi-Fuji Technical Center?
Hiroshi Tada, Project Manager, Motor Sports Division:It really varies, with some people coming from a production car development background, and then some who leave race engine work for assignments in production. The same goes for me, but there is a definite back-and-forth of technology as people move from assignment to assignment. Involvement in F1 engine development at Higashi-Fuji increases an engineer’s technical level, which can then be applied back in the production car environment, and vice-versa. |
 |
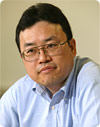 |
|
Project Manager:
Hiroshi Tada |
|
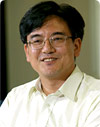 |
 |
Engine Testing:
Kozo Matsuura |
|
|
Kozo Matsuura, Project Manager, Motor Sports Division:There was an in-house announcement recruiting engineers for the F1 program. At that time, I was working on developing technology related to fuel cells. Fuel cells are technology with a bright future, and the work was interesting, but I decided to volunteer for F1, believing that a varied background could only help my career in the long run. I feel like now I have to take the skills I have learned here in the F1 program and put them to use somehow in the future. |
Masahiro Moritani, Project Manager, Motor Sports Division:Involvement in the very demanding world of motorsports really hones your skills. It’s an extremely effective environment for developing as an engineer. Just looking at my own group, there’s me from a drive systems background, and others from testing, suspension, production technology and several other departments. |
 |
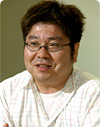 |
|
Project Manager:
Masahiro Moritani |
|
How do you exchange information with TMG?
Matsuura:There’s a video conference once every two weeks just for engine-related work alone.
Nagai: Also, staff members from the Motor Sports Division take turns traveling to TMG for short trips on an as-needed basis.
Moritani: There’s a weekly meeting with TMG covering aerodynamics. Advanced development is our main focus, but it can take quite a while to perform calculations, so there are times when we support TMG with development of a current iteration. We communicate back and forth via video conferencing.
|
1. Engine Simulation Tests
A deafening roar of an F1 engine comes from one room of the laboratory building. The constant up-shifting and down-shifting makes it sound like the engine’s actually being raced around an F1 circuit, which might be why they call it “Circuit Pattern Simulation” testing.
|
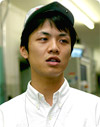 |
 |
Engine Simulation: Shinnosuke Sato |
|
|
Shinnosuke Sato, Motor Sports Division:We use actual data collected from our cars on the circuits to reproduce racing conditions for reliability testing. The test menu we are using right now is from the pre-modified Hockenheim circuit. We think it’s a good evaluation, since the burden on the engine, including the amount of time on full throttle, is very high. Besides Hockenheim, we also recreate conditions at Spa Francorchamps, Suzuka, Indianapolis and others. |
|
|
|
What are the benefits of this kind of testing?
Sato:For example, when we’re conducting circuit pattern testing, we can measure the conditions of the pistons at certain intervals. This has given us one way to find solutions under near race-like conditions.
|
 |
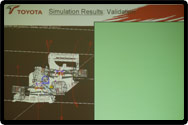 |
|
CFD Application Screen |
2. CFD
The Higashi-Fuji Technical Center also conducts full-scale chassis development. One representative example of this work is CFD. CFD is an abbreviation for Computational Fluid Dynamics, and has to do with techniques for visualizing air flow that can’t normally be seen with the naked eye. Using this technique, engineers analyze the flow of air around, over and under the chassis, and the resulting data is incorporated into the design of wings and other body parts.
|
Yasutake Haramoto (Dr.Eng.), Assistant Manager, Motor Sports Division:To make an F1 car faster, we increase downforce (force pushing the car down to the surface of the track). Downforce and reducing air resistance are the two most important factors in this area. At the Higashi-Fuji Technical Center, we conduct coordinated development with TMG, looking at implementation several races down the line. In addition, we conduct research into principles into so-called advanced development, discovering what we can do to improve the efficiency of the car. For example, we recently received a request from TMG to investigate the aerodynamic effects of certain parts under CFD. We conducted verification tests here, and sent the feedback to TMG in Germany. |
 |
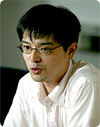 |
|
Assistant Manager:
Yasutake Haramoto |
|
Are there any particular episodes from the 2005 season that stand out in your mind?
Haramoto:One way to increase the flow of cooling air is to change the setting of the louver. But aerodynamic performance can be degraded depending on where the louver is installed. We really struggled with increasing cooling air flow without losing the downforce value. When the TMG wind tunnel ultimately confirmed our results, I was extremely relieved.
3. Other Research and Development
We have introduced some specific examples of advanced F1 development at the Toyota Higashi-Fuji Technical Center. But there is a variety of other research going on at the same time, providing critical support to TMG.
|
Please tell us about your work.
Junya Tanaka, (intake and exhaust systems development) Motor Sports Division:I do research and development on intake and exhaust system parts, including the intake port, exhaust port, combustion chamber configuration and so forth. The intake port is the route through which air is brought into the engine. Performance can change significantly according to the configuration. I use a computer to analyze what configuration leads to the best performance. We also conduct analysis to optimize the configuration of the exhaust ports and the combustion chamber.
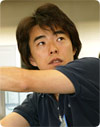 |
 |
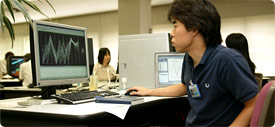 |
Intake and Exhaust Systems Development:
Junya Tanaka |
Intake and Exhaust Systems Simulation |
Kousaku Kawakita, Project Manager (valve operation system development), Motor Sports Division:We conduct tests by installing a valve operation system, in other words intake and exhaust valves, pneumatic system, cams and so on, on an actual cylinder head. We look for new ideas and propose them to TMG. The more air you can get to the engine, the stronger the combustion and RPM output, which leads to greater horsepower out of the engine. At high revolutions, the valves must open and close exactly as designed. At the same time, we try to hold down friction, which reduces loss and increases horsepower. Our job is to find the best valve operation solution to meet these demands.
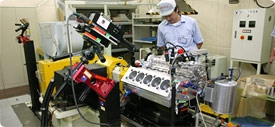 |
 |
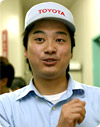 |
Valve Operation System |
Valve Operation System Development:
Kousaku Kawakita |
Naoyuki Ieda, Assistant Manager (single-cylinder performance testing), Motor Sports Division:We use a single-cylinder engine for advanced development, focusing particularly on combustion analysis and combustion improvement using leading-edge measurement technologies. As cars get faster each year, winning is not a matter of only horsepower, but fuel efficiency as well. Better fuel efficiency leads to more freedom in planning race strategy, which leads to better stronger finishes. So you see, fuel efficiency is very important even in racing.
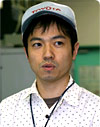 |
 |
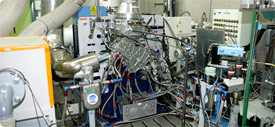 |
Single-Cylinder Performance Testing:
Naoyuki Ieda |
Single-Cylinder Performance Testing |
Toshio Takaoka, Project Manager (dual-axis bench testing), Motor Sports Division:We conduct circuit simulations using gearboxes from the actual race cars. Taking measurements as close as possible to the conditions of the actual car helps us consider overall chassis control. Thanks to our V10 test machines, we’ve been able to build an engine that won’t break down, and operating a dual-axis bench will help us make a gearbox that won’t break, either.
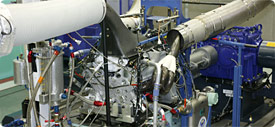 |
 |
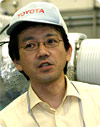 |
Dual-Axis Bench Testing |
Dual-Axis Bench Testing:
Toshio Takaoka |
|
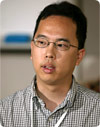 |
 |
Chassis Movement Analysis:
Tomohiko Miura |
|
|
Tomohiko (Max) Miura, Motor Sports Division (chassis movement analysis):I use simulation tools to reproduce the movement of a chassis, which leads to greater chassis development efficiency. The chassis movement analysis tools allow us to predict behavior, such as how a suspension arm flexes, before the car is actually driven. |
Kenji Sumi, Project Manager (chassis movement analysis), Motor Sports Division:Ultimately, chassis movement analysis is conducted mostly for the tires. We conduct simulations focused on the tires, based on suggestions as to the optimal suspension layout. We are looking at things from a somewhat longer-rage viewpoint than the set up for the race next week or the week after. |
 |
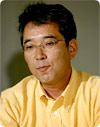 |
|
Chassis Movement Analysis:
Kenji Sumi |
|
|
Looking over the activities at the Toyota Higashi-Fuji Technical Center, one can see the valuable role the Center plays in F1 car development. Even though operations are spread over the long distance between Japan and Germany, the two sites act substantially as one. The process mobilizes the collective effort of Toyota as it expands further throughout the world.
There are also those within the production departments near Toyota Motor Corporation headquarters involved in the F1 program. They manufacture the main parts of the engine—cylinder heads, cylinder blocks and crank shafts. Machines can be used to achieve a certain level of production precision, but ultimately a master’s touch is required. In the end, let us note that these parts, finished through the skills and techniques of these master technicians, are sent to TMG.
While they may work quietly off-stage, out of the public spotlight, there are actually many dedicated, hardworking Japanese staff members that play vital roles in supporting TMG activities.
| |
|
|